Blog #5: (Le)ts (go)-yo
- Team
- Oct 23, 2019
- 2 min read
Updated: Oct 31, 2019
Over the past two weeks, our team has finalized parameters, tested thermoforms, and machined our first mold! Follow along to get all the details on what we've done.
Thermoform:
After the past design review, we learned that we can use the formlabs to 3D print our mold. Given that we no longer had to design around machinability (just print-ability), we reversed some adjustments were done for DFM. For our Lego logo, we reverted to the full, bubbly form and 3D printed. Our main concerns with 3D printing were two fold: 1) could a 3D printed piece withstand the heat without deformation in the thermoformer and 2) could a 3D printed piece withstand the vacuum pressure in the thermoform. After testing, we determined that these are not concerns and that the 3D molds would work great!
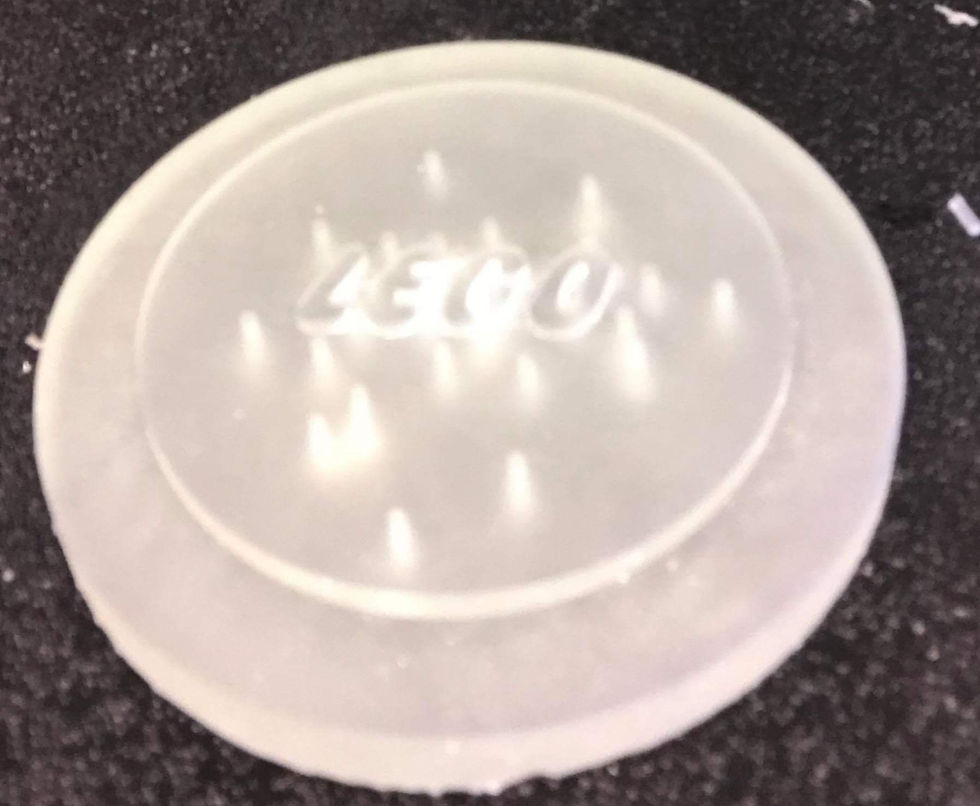
However, the form and resolution of the part is worrisome from a visual point of view. We hope to look into coloring the 3D printed part (similar to the surfer yoyo from a past year) in order to get contrast and make the logo visually appealing.
Critical Mold:
We have manufactured our front Lego mold. This is our most critical part as it the function of the Lego studs and ability to use our yoyo in conjunction with actual Legos is a key aspect to fix early on. We plan to purchase a lego set to assist in testing of our parts.
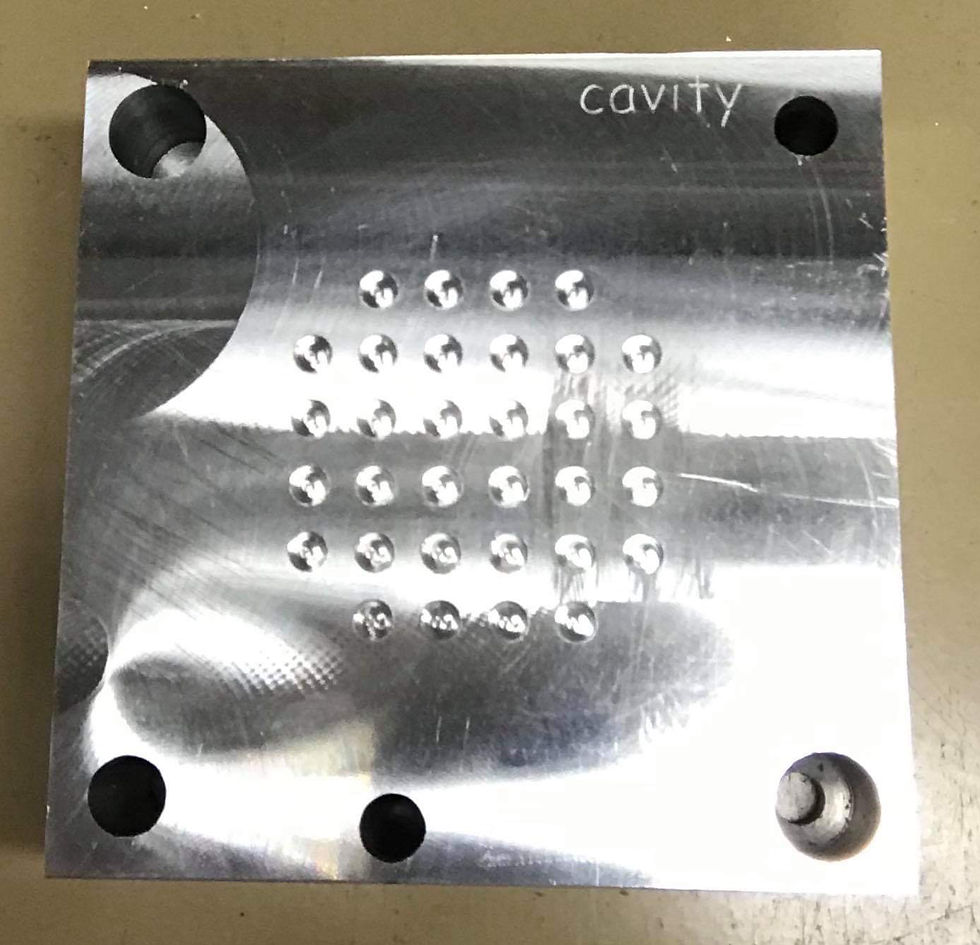

Shrinkage:
We have also found appropriate shrinkage parameters for each of our parts and have implemented these parameters into our mold making. We found on average that shrinkage for our covers is around 2-3% shrinkage and have implemented this in our mold making.
CAD/CAMS:
Our group has also finalized all the CADs for our parts, made the CADs for all of our molds, and also finished CAMs for each of these mold. Essentially, all of our parts are a the machining stage which we hope to finish quickly and get into testing.
Comments